Bevel gearboxes KTM
Type: KTM
Size: 3 – 7
Gear ratio: „i“ = 5,9 – 300
Output: 0,37 – 30 kW
Torque: 100 – 2500 Nm
Information on the product
Concept
The proper concept of gearboxes adopted by the manufacturer’s designing department has been developed with the help of computer-aided technology and high-quality computing programs. The computer-aided design technology (CAD) has also developed the drawing and accompanying documentation. The result is a product of optimum dimensions and function parameters.
Compactness
Integrated gearing has made it possible to reduce the gearbox dimensions. Accurate gearing machining reduces vibrations and ensures silent operation.
Adaptability to clients’ requirements
Large number of combinations of inlet and outlet shafts and flanges make it possible to use the TOS gearboxes for almost all of the required modes of drives.
Variability
The gearbox form makes easier the attachments to all types of devices.
Fine graduation of gears
Configuration of gears and their fine graduation from i = 5,9 enable the accurate selection of the required outlet revolutions.
Motors
Gearboxes are normally provided with motors made by SIEMENS Company.
Surface treatment
The gearboxes are provided with priming coat and sprayed polyurethane varnish. In KTM gearboxes the varnish spraying unifies the color of the motor attached.
Lubrication
The gearbox gearings are lubricated with synthetic oil. The standard oil filling has been provided in cooperation with ÖMV.
Smooth change of revolutions
If smooth change of revolutions, steady speed or steady torque are required, the KTM gearboxes should be fitted with frequency converters.
Type identification
The gearbox is univocally specified with the type designation. Therefore, the order must include the complete designation with the numerical code as shown in the pattern. When ordering, it is possible to use the order form included in the chapter 12 where even the requirements differing from the standard supplied may be stated.
Type
KTM is a designation of the spur bevel gearboxes manufactured by TOS ZNOJMO
Designation
is given with the size 3 – 6 – Table 2.1.
Size | Three-stage (KTM_3) designation |
Ø of the output (hollow) shaft |
---|---|---|
KTM 33 | 33 | Ø 30 (35) |
KTM 43 | 43 | Ø 40 |
KTM 53 | 53 | Ø 50 |
KTM 63 | 63 | Ø 60 |
KTM 73 | 73 | Ø 70 |
Box position
the gearbox form and style make it possible to use the gearboxes in different operating positions, as shown in Table 2.2. Code numbers 1 to 6 specify the position.
Table 2.2
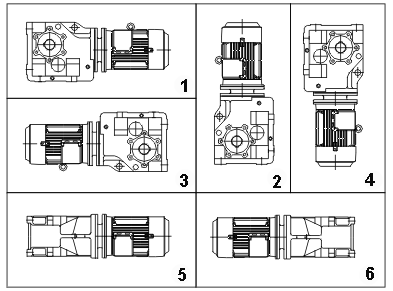
Input design:
- with the pin at the outlet
- with an electric motor attached.
- without flanged electric motor IM 3641 FT** (IM B14 FT** ) – smaller flange B14 A
- without flanged electric motor IM 3641 FT** attached ( IM B14 FT** ) – bigger flange B14 B
- without flanged electric motor IM 3041 ( IM B5 )attached
- Flange dimensions and their combinations with gearboxes are included in Tables 8.2 and 8.3.
Outlet style:
- Massive shaft to the left version, chapter 7.1
- Massive shaft to the right version, chapter 7.1
- Hollow shaft basic version, chapter 7.2
- Massive shaft and outlet flange to the left version, chapter 7.3
- Massive shaft and outlet flange to the right version, chapter 7.3
- Hollow shaft and outlet flange to the left version, chapter 7.4
- Hollow shaft and outlet flange to the right version, chapter 7.4
![]() |
![]() |
![]() |
![]() |
![]() |
![]() |
![]() |
![]() |
Ratio „i“
in conformity with the individual types specified in the output table
Electric motor type designation and its output P1:
conforming with Table 8.1. or the electric motor output P1 conforming with Table 6.1. (see Output parameters)
Example of type designation
a) spur bevel gearbox …………………………………………………………………………………………. | KTM X X X X X |
b) gearbox size 5 ……………………………………………………………………………………………….. | KTM 5 X X X X |
c) three-stage gearing ………………………………………………………………………………………….. | KTM 5 3 X X X |
d) horizontal position of the shaft axis, motor horizontally as per Table 2.2 …………………….. | KTM 5 3 1 X X |
e) with electric motor ………………………………………………………………………………………….. | KTM 5 3 1 2 X |
f) without any attaching flange at the outlet ……………………………………………………………….. | KTM 5 3 1 2 1 |
g) ratio i = 121,9 …………………………………………………………………………………………………. | i = 121,9 |
h) electric motor axis height 90, 4-pole, power 1,5 kW ……………………………………………… | 90 4, 1,5 kW |
Additional requirements may be specified in the buying order sheet.
Correctness of gearbox parameters selection can be verified according to chapter 4 – draft of the gearbox size
Mounting style
Spur bevel gearboxes KTM are supplied with the electric motor required by the customer or as
a free shaft-end version or inlet hollow-shaft version, in dimensions meeting the IEC stipulations.
In case a KTM version without motor attached is required, the electric motor shaft diameter shall be specified in the buying order together with the flange dimension (pitch circle of attaching holes). For selecting the motor, the user should consult the chapter „Electric motors“ where combinations of output, speed, axis height conforming with IEC and other dimensions of electric motors. For detailed information on electric motors see the self-standing catalogue provided by the of electric motor manufacturer.
Rated powers
The table specifies the values of power P1 together with their respective values of output / torques Mk2 that the gearboxes are able to transmit. These values have been fixed for uniform, impact-free loads of the gearbox – for the operating coefficient Sm=1, at nominal revolutions n1=1400 min-1.
Table 5.1.
Performance data
The table includes gearboxes ordered conforming the gear ratio for the given output of the driving electric motor. For nominal power and electric motor speed n1=1400 r.p.m. the torque M2 and output speed n2, service factor Sf and admissible output hollow shaft load Fr.
Table 6.1. Power tables of KTM gearboxes
Dimensions [MM]
Electric motors
Motor mounting position – terminal board standard location in position 1. Another position of the terminal board shall be indicated in the order, specified as a special requirement.
The chapter of electric motors involves basic technical and dimensional data of the motors of 56 to 160 axis height supplied by Siemens Mohelnice electric motor manufacturer. For additional or more detailed technical information ask for a self-contained motor manufacturer’s catalogue.
Shape– flange type IM 3041 (IM B5), IM 3641 FT**, IM 3641 FT**)- foot-flange type IM 2081 (IM B35)- all assembly shapes according too IEC 34-7 code I/II
Mounting dimensions– in compliance with IEC 72 / DIN 42673
Protection– IP 55
Table 8.2 Motors dimensional parameters [mm]
Type | flanged motor – dimensions in mm | ||||||||||||||||||
---|---|---|---|---|---|---|---|---|---|---|---|---|---|---|---|---|---|---|---|
height axesy | AC | HF | HG | L | LA | LB | LD | LG | LK | M | N | P | S | T | D | E | F | G | GD |
71 | 139 | 88,5 | 111 | 240 | 9 | 210 | 63,5 | 75 | 32 | 130 | 110 | 160 | 10 | 3,5 | 14 | 30 | 5 | 11 | 5 |
80 | 156,5 | 95,5 | 120 | 272,5 | 10 | 232,5 | 63,5 | 75 | 32 | 165 | 130 | 200 | 12 | 3,5 | 19 | 40 | 6 | 11 | 6 |
90S | 173,6 | 105,5 | 128 | 331 | 10 | 281 | 79 | 75 | 32 | 165 | 130 | 200 | 12 | 3,5 | 24 | 50 | 8 | 15,5 | 7 |
100L | 196 | 78 | 129 | 327,5 | 11 | 312,5 | 102 | 120 | 42 | 215 | 180 | 250 | 14,5 | 4 | 28 | 60 | 8 | 20 | 7 |
112M | 219,5 | 91 | 142 | 393 | 11 | 333 | 102 | 120 | 42 | 215 | 180 | 250 | 14,5 | 4 | 28 | 60 | 8 | 24 | 7 |
132S | 259 | 107 | 164 | 454 | 12 | 374 | 128,5 | 140 | 42 | 265 | 230 | 300 | 14,5 | 4 | 38 | 80 | 10 | 24 | 8 |
132M | 259 | 107 | 164 | 454 | 12 | 374 | 128,5 | 140 | 42 | 265 | 230 | 300 | 14,5 | 4 | 38 | 80 | 10 | 33 | 8 |
160M | 314 | 127 | 191 | 588 | 13 | 478 | 160,5 | 165 | 54 | 300 | 250 | 350 | 18,5 | 5 | 42 | 110 | 12 | 33 | 8 |
160L | 314 | 127 | 191 | 588 | 13 | 478 | 160,5 | 165 | 54 | 300 | 250 | 350 | 18,5 | 5 | 42 | 110 | 12 | 37 | 8 |
180 | 364,0 | 81 | 262 | 670 | 13 | 560 | 157 | 152 | 300 | 250 | 350 | 18,5 | 5 | 48 | 110 | 14 | 42,5 | 9 | |
200 | 402 | 164 | 300 | 720 | 15 | 610 | 196 | 260 | 350 | 400 | 18,5 | 18,5 | 5 | 55 | 110 | 16 | 48,8 | 10 |
Type | flanged motor – dimensions in mm | ||||||||||||||||||
---|---|---|---|---|---|---|---|---|---|---|---|---|---|---|---|---|---|---|---|
Design IM B5 | DesignIM B14T.. smaller | Design IM B14T.. bigger | |||||||||||||||||
axis height | gearbox size | M | N | P | S | T | LA | vel.př. | M | N | P | S | T | gearbox size | M | N | P | S | T |
71 | FF130 | 130 | 110 | 160 | 10 | 3,5 | 9 | – | – | – | – | – | – | FF100 | – | – | – | – | – |
80 | FF165 | 165 | 130 | 200 | 12 | 3,5 | 10 | FT100 | – | – | – | – | – | FF130 | 130 | 110 | 160 | M8x20 | 3,5 |
90S | FF165 | 165 | 130 | 200 | 12 | 3,5 | 10 | FT115 | – | – | – | – | – | FF130 | 130 | 110 | 160 | M8x20 | 3,5 |
100L | FF215 | 215 | 180 | 250 | 14,5 | 4 | 11 | FT130 | 130 | 110 | 160 | M8x20 | 3,5 | FT165 | 160 | 130 | 200 | M10x24 | 3,5 |
112M | FF215 | 215 | 180 | 250 | 14,5 | 4 | 11 | FT130 | 130 | 110 | 160 | M8x20 | 3,5 | FT165 | 160 | 130 | 200 | M10x24 | 3,5 |
132S | FF265 | 265 | 230 | 300 | 14,5 | 4 | 12 | FT165 | 160 | 130 | 200 | M10x24 | 3,5 | – | – | – | – | – | – |
132M | FF265 | 265 | 230 | 300 | 14,5 | 4 | 12 | – | – | – | – | – | – | – | – | – | – | – | – |
160M | FF300 | 300 | 250 | 350 | 18,5 | 5 | 13 | – | – | – | – | – | – | – | – | – | – | – | – |
160L | FF300 | 300 | 250 | 350 | 18,5 | 5 | 13 | – | – | – | – | – | – | – | – | – | – | – | – |
180 | FF300 | 300 | 250 | 350 | 18,5 | 5 | 13 | – | – | – | – | – | – | – | – | – | – | – | – |
200 | FF350 | 350 | 300 | 450 | 18,5 | 5 | 16 | – | – | – | – | – | – | – | – | – | – | – | – |
Table 8.3 Possibility of providing the gearbox with a motor flange
Motor | 71 | 80 | 90 | 100 | ||||||||
---|---|---|---|---|---|---|---|---|---|---|---|---|
Shaft dia | 14 | 19 | 24 | 28 | ||||||||
IEC | B14A | B14B | B5 | B14A | B14B | B5 | B14A | B14B | B5 | B14A | B14B | B5 |
Flange size | M=85 | M=115 | M=130 | M=100 | M=130 | M=165 | M=115 | M=130 | M=165 | M=130 | M=165 | M=215 |
KTM 33 | ♦ | ♦ | ♦ | ♦ | ♦ | ♦ | ♦ | ♦ | ♦ | ♦ | ||
KTM 43 | ♦ | ♦ | ♦ | ♦ | ♦ | ♦ | ♦ | |||||
KTM 53 | ♦ | ♦ | ♦ | ♦ | ♦ | ♦ | ♦ | |||||
KTM 63 | ♦ | ♦ | ♦ | ♦ | ♦ | ♦ | ♦ | |||||
KTM 73 | ♦ | ♦ | ♦ | ♦ | ♦ | ♦ | ♦ |
Motor | 112 | 132 | 160 | 180 | 200 | ||||||
---|---|---|---|---|---|---|---|---|---|---|---|
Shaft dia | 28 | 38 | 42 | 48 | 55 | ||||||
IEC | B14A | B14B | B5 | B14A | B14B | B5 | B14A | B14B | B5 | B5 | B5 |
Flange size | M=130 | M=165 | M=215 | M=165 | – | M=265 | – | – | M=300 | M=300 | M=300 |
KTM 33 | |||||||||||
KTM 43 | ♦ | ♦ | ♦ | ♦ | ♦ | ||||||
KTM 53 | ♦ | ♦ | ♦ | ♦ | ♦ | ♦ | |||||
KTM 63 | ♦ | ♦ | ♦ | ♦ | ♦ | ♦ | |||||
KTM 73 | ♦ | ♦ | ♦ | ♦ | ♦ |
Lubrication
Lubrication of gear sets and bearings is indispensable for ensuring reliable gearbox operation along its whole service life. Suitable lubrication provides for high efficiency, essential wear restriction, and silent operation. The KTM gearboxes are normally filled with high-quality synthetic oil as a service-life filling. Therefore, the gearbox housings must not be fitted with filling, checking, and drain holes. Informative quantity of lubricating fillings for the various sizes are specified in Table 10.1.
Tab. 10.1.
oil quantity [ l ] | ||||||
---|---|---|---|---|---|---|
type | position 1 | position 2 | position 3 | position 4 | position 5 | position 6 |
KTM 33 | 0,7 | 1,4 | 1,2 | 1,1 | 1,1 | 1,1 |
KTM 43 | 1,6 | 2,9 | 2,4 | 2,2 | 2,6 | 2,6 |
KTM 53 | 1,8 | 5,2 | 4,2 | 3,9 | 4,2 | 4,2 |
KTM 63 | 2,5 | 9,6 | 8,5 | 7,6 | 7,5 | 7,5 |
KTM 73 | 7,5 | 19,0 | 12,0 | 12,0 | 12,0 | 12,0 |
Use of synthetic lubricants we normally supply, is recommended, nevertheless the use of mineral oils is also possible. Suitable lubricating fillings (equivalents from different manufacturers) are specified in Tab. 10.2.
Tab. 10.2.
mineral oils | synthetic oils | |||
---|---|---|---|---|
surrounding temperature | -10 oC – +50 oC | -10 oC – +50 oC | ||
type of load | normal | heavy | normal | heavy |
Agip | Blasia 220 | Blasia 320 | Blasia S | |
Aral | Degol BG 220 | Degol BG 320 | Degol GS 220 | |
Castrol | Alpha SP 220 | Alpha SP 320 | Alpha SH 220 | |
ESSO | Spartan EP 220 | Spartan EP 320 | ||
Klüber | Lamora 220 | Lamora 320 | Syntheco HT 220 | |
Mobil | Mobilgear 632 | Mobilgear 634 | SHC 630 | |
Shell | Omala EP 220 | Omala EP 320 | Omala HD 220 | |
OMV | Ole HST 220 EP | Ole HST 320 EP | Unigear S 75 W-90 | |
Optimol | Optigear BM 220 | Optigear BM 320 | Optigear A 220 | |
Total | Carter EP 220 | Carter EP 320 | ||
Paramo | Paramol CLP 220 | Paramol CLP 320 |
For medium and light operation and lower surrounding temperature, the mineral oils specified are included in ISO-VG 220 viscosity class; for heavy duty and higher surrounding temperatures, they are included in ISO-VG 320 viscosity class.
Lubricating fillings should be exchanged, in the case of mineral oils, after the first 400 operating hours and then after every 4000 hours of operation.
Warning
Synthetic and mineral lubricants may not be mixed. Even mixing synthetic products of different manufacturers may be problematic. In case of passing to another type or mark of lubricant, the gearbox must be cleaned unconditionally.
Accessories
Output shaft
Single or double sided output shaft may be inserted into the hollow shaft.
Single sided shaft
Double sided shaft
Type KTM | A | A1 | Ø Dh7 | Ø D1 | L | L1 | EV | C | Z1 | Z2 | F |
---|---|---|---|---|---|---|---|---|---|---|---|
KTM 33 | 112 | 216 | 35 | 45 | 178 | 281 | 60 | 5 | M12 | M12 | 10 |
KTM 43 | 138 | 260 | 40 | 46 | 228 | 352 | 80 | 10 | M16 | 12 | 12 |
KTM 53 | 165 | 302 | 50 | 58 | 265 | 402 | 90 | 10 | M16 | 14 | 14 |
KTM 63 | 185 | 350 | 60 | 68 | 305 | 470 | 110 | 10 | M20 | M20 | 18 |
KTM 73 | 250 | 442 | 77 | 88 | 410 | 602 | 140 | 20 | M20 | M20 | 20 |
Coupling shaft
The KTM gearboxes may be provided – on special customer’s request – with a suitable type of shaft slip coupling at the output (or the input) for compensating the radial, axial, and angular misalignment of the shaft for limiting the transmission torque, or with an overrunning clutch, or with combination of elastic coupling with slid coupling and of elastic coupling with the overrun clutch.
Reaction arm
Type KTM | A | B | C | Ø D | F | G | J | Ø H | Ø E |
---|---|---|---|---|---|---|---|---|---|
KTM 33 | 200 | 65 | 298 | 80 | 14 | 24 | 6 | 8,4 | 100 |
KTM 43 | 230 | 65 | 330 | 90 | 14 | 24 | 6 | 11 | 110 |
KTM 53 | 300 | 85 | 425 | 110 | 16 | 26 | 8 | 17 | 142 |
KTM 63 | 350 | 105 | 500 | 140 | 25 | 30 | 8 | 17 | 175 |
KTM 73 | – | – | – | – | – | – | – | – | – |
Storage, putting into operation, mainenance
Storage
When dispatched from the manufacturer’s, the external functional surfaces are protected against atmospheric corrosion with a short-term preserving spray coating. Should the gearbox be stored for a longer period of time remaining out of operation, it is indispensable – depending on the environmental conditions – to reapply the preservation. In the case of a long-term storage, the gearbox must be filled with oil in the amount stated in chapter “ lubrication„.
The storage compartment has to be dust-free as far as possible and dry. The storage compartment should not exceed the limits of 0 to 40 °C. It is recommended to rotate the outlet shaft through at least one turn every 3 to 4 months.
The gearboxes have to be transported and stored in the mounting position.
Mounting, putting into operation
When installing the gearbox, take care to:
– to remove any obstacles restricting the air flow and heat sources from the nearness of the spur gear unit.
– to make use of protecting switches in the case of impact loads, and of overload couplings. Omission of these measures may result in the gearbox damage.
– to mount the joined coaxial shafts and couplings in accordance with the respective operating instructions from the coupling/ clutch supplier.
– to mount the gearbox on a flat and machined surface.
– to lock the components slipped over the shaft against loosening.
– to protecting the gearboxes against extreme weather inclemency.
– to check the oil quantity – and replenish it if necessary.
Shaft sealing
Satisfactory gearbox operation also depends on the correct function and conditions of the shaft sealing. Service life of the shaft sealing is heavily influenced with the temperature of contact surroundings, potential chemical reactions, which arise between the sealing material components and lubricants. The shaft sealing should be replaced if damaged and disabled to accomplish its function.
Photogallery
Výkresy a 3D modely
Výkresy převodovek KTM25A, motor IEC 71
Převodovka KTM25A, motor IEC 71, příruba motoru M=115, provedení U | ||
---|---|---|
ktm25a-71-115-u.dwb | ktm25a-71-115-u.exe | |
ktm25a-71-115-u.dwg | ktm25a-71-115-u.step.zip | |
ktm25a-71-115-u.dxf | ktm25a-71-115-u.sldprt | |
Převodovka KTM25A, motor IEC 71, příruba motoru M=130, provedení U | ||
ktm25a-71-130-u.dwb | ktm25a-71-130-u.exe | |
ktm25a-71-130-u.dwg | ktm25a-71-130-u.step.zip | |
ktm25a-71-130-u.dxf | ktm25a-71-130-u.sldprt |